PLANIFICACIÓN, SIMULACIÓN Y DIMENSIONAMIENTO DE RECURSOS
OPTIMIZACIÓN AVANZADA: DIMENSIONA TUS RECURSOS CON PRECISIÓN PARA MAXIMIZAR RENDIMIENTO
- Anticipación al exceso o déficit de recursos y a los cuellos de botella.
- Corrección del desequilibrio permanente entre carga y capacidad.
- Incremento de la capacidad de producción y mejora del nivel de servicio a los clientes.
- Reducción de costes por subactividad.
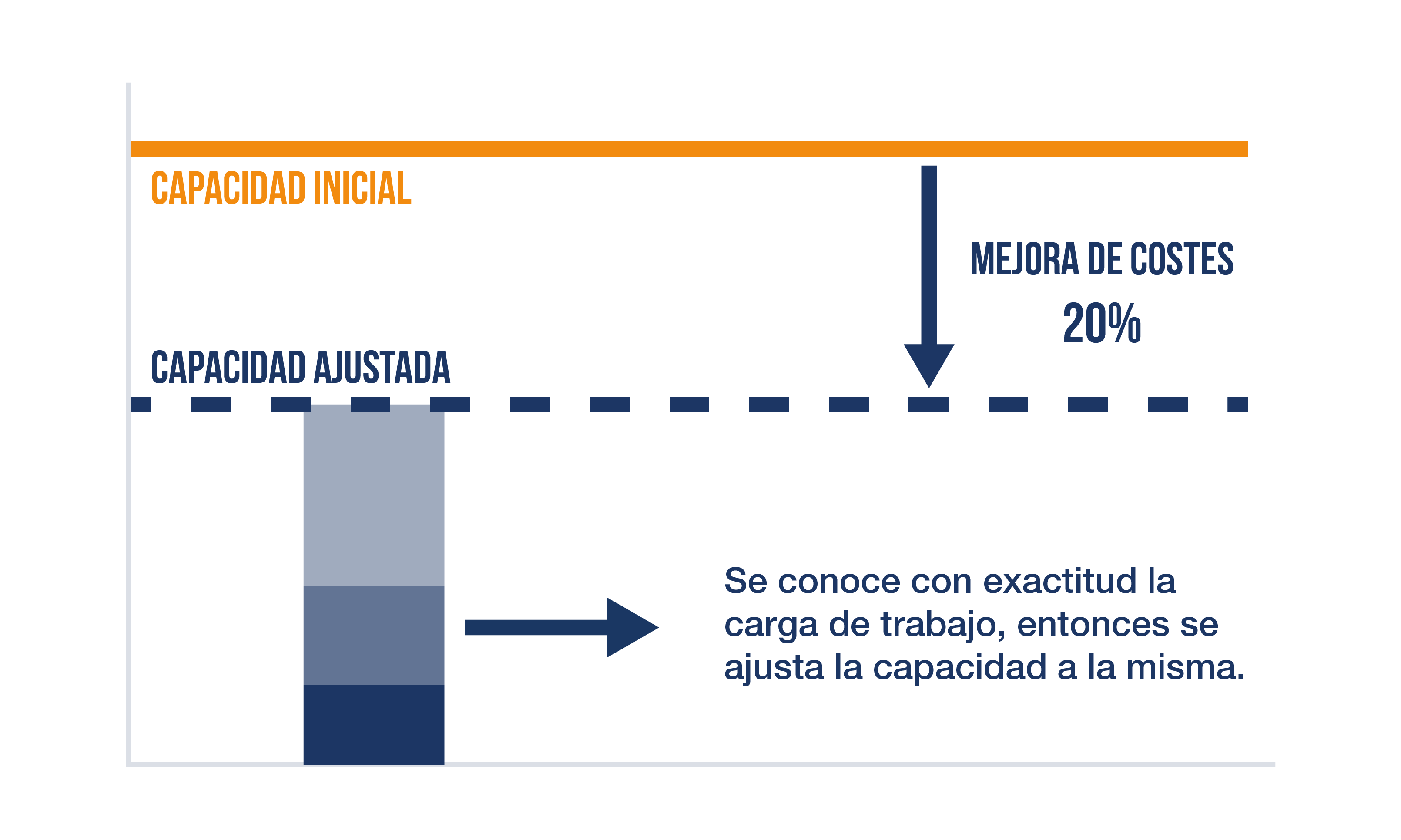
Definición del problema
- La reducción de la carga de trabajo merma los beneficios obtenidos en periodos de saturación normal.
- El dimensionamiento riguroso y cuantificado de la fábrica no existe. Se tiene la misma plantilla siempre y, si se calculan los recursos, se realiza de manera muy aproximada. De manera que se suele sobredimensionar.
- La saturación de cada operario o máquina se presupone.
- El mix de producción es muy variado y genera gran dificultad en la planificación.
- Las tediosas planificaciones que se elaboran requieren horas de dedicación y su validez tiene muy poca duración (ya sea por una incidencia, una urgencia, etc). Esto crea frustración y provoca que no se replanifique la siguiente situación o que se haga de manera muy aproximada.
Causas
- No se tienen tiempos estándar o velocidades de línea estándar.
- No se dispone de una herramienta que permita planificar de manera ágil los trabajos, se hace de manera manual, mentalmente o sencillamente no se hace.
- Cuando se planifica, cuesta tanto trabajo, que no se replanifica ágilmente y no se reacciona a los cambios en las condiciones.
- La planificación se delega en el buen hacer de los encargados, ya que son quienes tienen contacto con los operarios.
- Esto lleva a una demanda casi permanente de más recursos.
- La optimización del orden de la fabricación se hace mentalmente y también se delega en los encargados.
- No se planifica teniendo en cuenta la saturación.
- No se planifican al detalle los cuellos de botella.
- No se genera un plan maestro de producción riguroso entre comercial y producción, por lo que, para cada periodo, o la fábrica está saturada o está ociosa.
Efectos
- El desequilibrio entre carga y capacidad de trabajo es el mayor causante del despilfarro en fabricación. Lo cual tiene numerosas implicaciones y de alto impacto.
- Se aumenta la capacidad más de lo necesario debido al desconocimiento de la carga real de trabajo y a la incertidumbre.
- Aun así, faltan recursos para cumplir el plan y los compromisos acordados con los clientes.
- Por lo que los encargados solicitan más personal.
- Personal que tras esa “sobrecarga” de trabajo, se vuelve “totalmente necesario” para la normalidad.
- O se resuelve mediante sobrecostes por horas extra.
- Los puestos o máquinas cuellos de botella provocan esperas en los puestos anteriores o posteriores.
- Incluso, a veces, se quedan parados sin trabajo… siendo cuellos de botella.
- Y la producción que no hace el cuello de botella no se puede recuperar.
- Urgencias y continuas replanificaciones.
- Lo que provoca un movimiento continuo de operarios entre puestos sin posibilidad de anticipación.
- Y un exceso de cambios de máquina, formato y de trabajo.
- Lo que a su vez provoca iniciar trabajos sin asegurar las condiciones estándar.
- Generando interrupciones continuas.
- Traduciéndose en sobrecostes por ineficiencias por incidencias.
- Trabajos que se preparan y se comienzan, se pausan, y vuelven a prepararse y a continuarse posteriormente.
- Operarios que, conociendo que la carga de trabajo asignada es baja, “estiran” el trabajo mediante ajustes y revisiones innecesarias, paradas, ausencias y baja actividad para que sea suficiente para acabar la jornada y no se le asignen más tareas.
- Los cambios de referencia no se planifican, por lo que siempre requieren un tiempo superior al estándar.
- Los pedidos no se agrupan generando lotes grandes de una misma referencia, por lo que se tienen más preparaciones de las que se debería.
- La fabricación no se ordena según criterios de eficiencia, por lo que no se optimizan los cambios ni la producción en función de la combinación óptima y la minimización de los tiempos de cambio y preparación.
- Y, además de lo anterior, del sobredimensionamiento de recursos, se incumplen los plazos de entrega.
- La fluctuación de la demanda que no se gestiona de manera ajustada provoca que los beneficios que se obtuvieron en periodos de saturación normal, queden mermados a causa de los periodos de baja carga de trabajo.
Necesidad y propuesta de solución
- 1. Definir un modelo y procedimiento de planificación y dimensionamiento orientado a:
- Servir los clientes según los acuerdos adoptados con estos.
- Al menor coste posible.
- 2. Definir políticas y acuerdos entre comercial y operaciones para garantizar las condiciones estándar de planificación y fabricación (política de pedidos urgentes, política de no interrupciones…).
- 3. Crear un maestro de tiempos/velocidades estándar según las referencias o familias de producto.
- 4. Definir una secuencia de producción que permita optimizar los cambios, produciendo en orden según la minimización de los tiempos de cambio.
- El simulador indicará el orden óptimo de fabricación, además de calcular los tiempos de cambio en función de la combinación escogida.
- 5. Desarrollar una herramienta de simulación y planificación de carga y capacidad que permita, a partir del mix de producción y de los recursos disponibles:
- Dimensionar los recursos y trazar una estrategia tomando decisiones en el largo plazo (6 meses – 1 año) gracias al cálculo de la carga de trabajo total de la fábrica y por secciones y puestos además de la saturación de los recursos.
- Dimensionar los recursos y trazar una estrategia tomando decisiones en el medio plazo (1 mes – 3 meses) gracias al cálculo de la carga de trabajo total de la fábrica y por secciones y puestos además de la saturación de los recursos.
- Ajustar, programar y asignar trabajos con hitos de inicio y fin en el corto plazo (día y horas) gracias al cálculo de la carga de trabajo por secciones y puestos además de la saturación de los recursos.
- Calcular de manera automática los plazos necesarios para ejecutar los trabajos.
- Crear un modelo de asignación de los trabajos en el corto plazo a los operarios para conocer su carga de trabajo y su saturación y así evitar sobrecostes diarios. Esta asignación es una guía de seguimiento para los operarios y mandos intermedios, quienes deberán minimizar las desviaciones con respecto a lo programado a corto plazo para cumplir con el plan de producción.
- Conocer los costes de mano de obra de cada planificación.
- A partir de distintos escenarios de mix de producción, conocer la carga de trabajo en valor absoluto y porcentual de cada familia de producto, sección, puesto, línea… en el corto, medio y largo plazo.
- 6. Generar un listado de amortiguadores de carga y capacidad para cada escenario que permita a la cadena de mando y a la dirección tomar decisiones para la resolución de los dos posibles escenarios:
- Capacidad sobrante u ociosa.
- Capacidad deficitaria.
- 7. Formar a los usuarios en los conceptos de planificación, gestión y productividad y en la utilización de la herramienta.
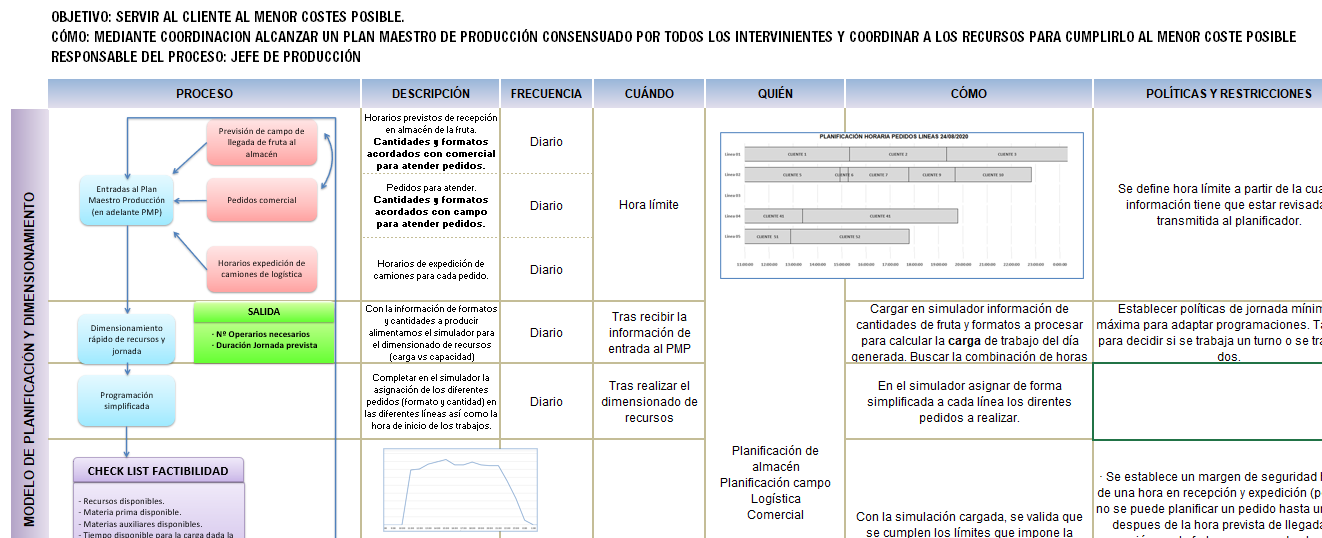
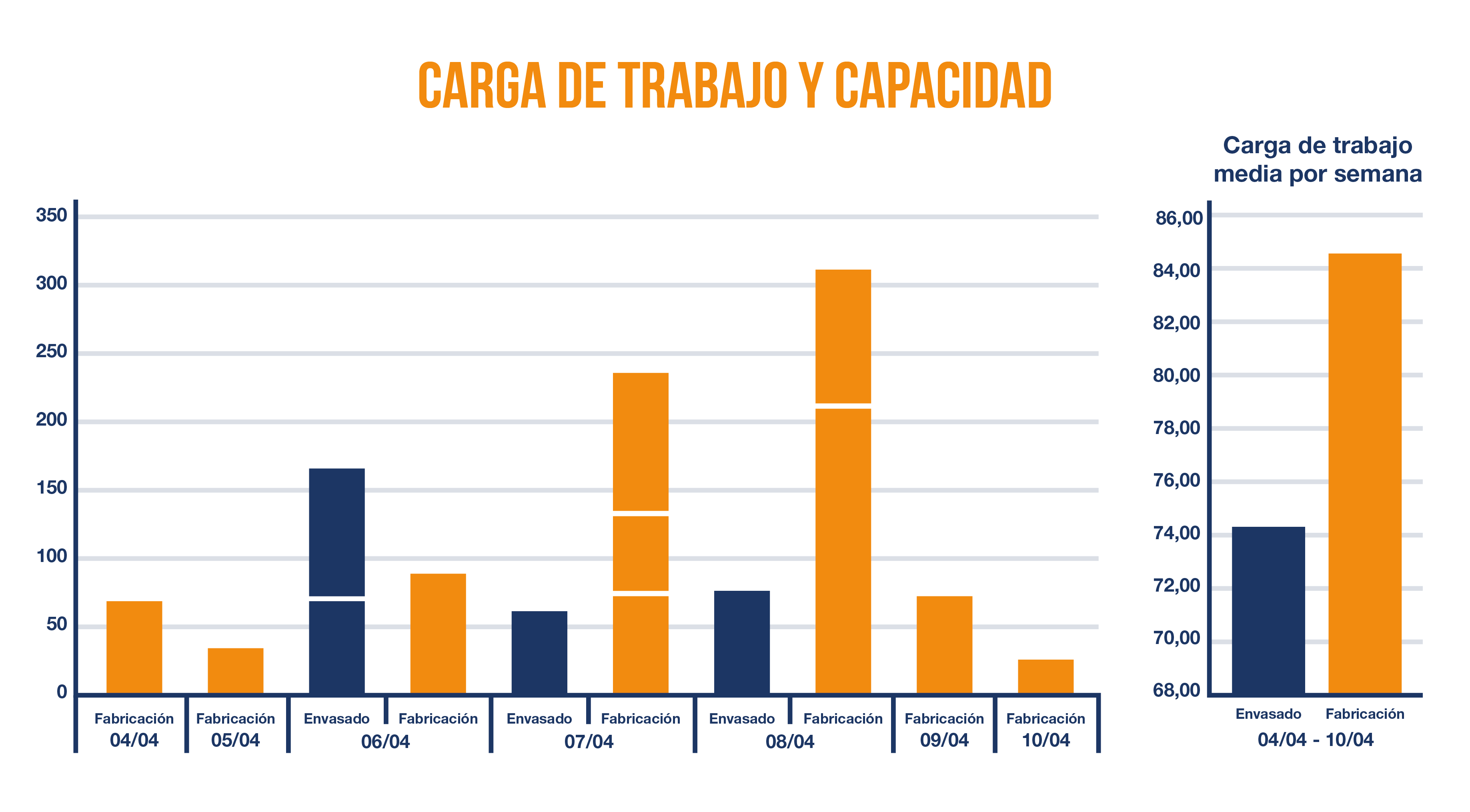
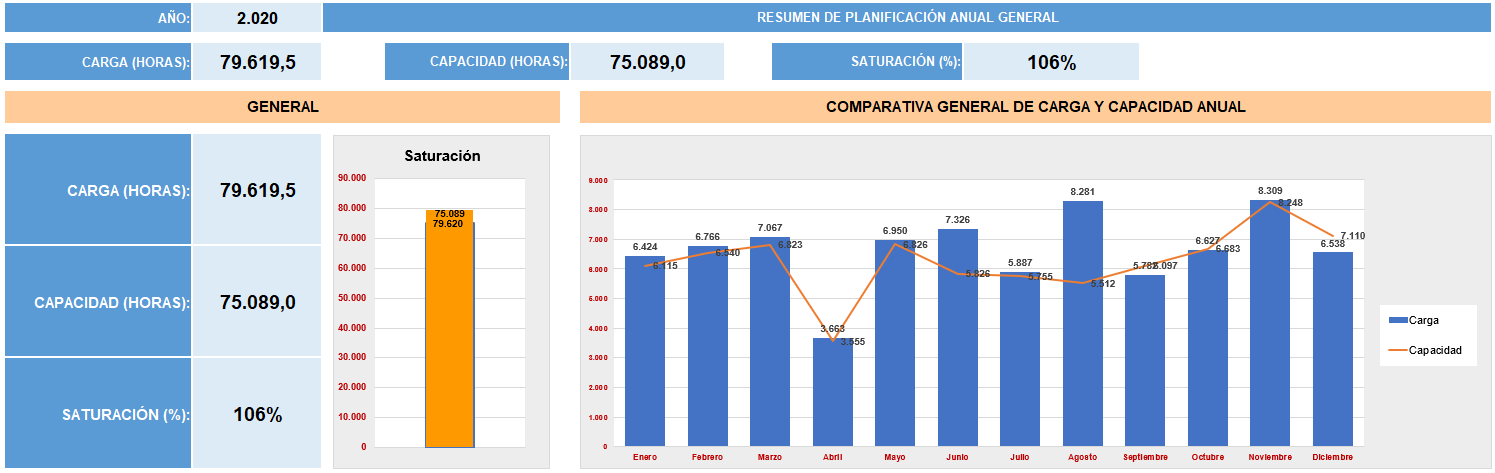
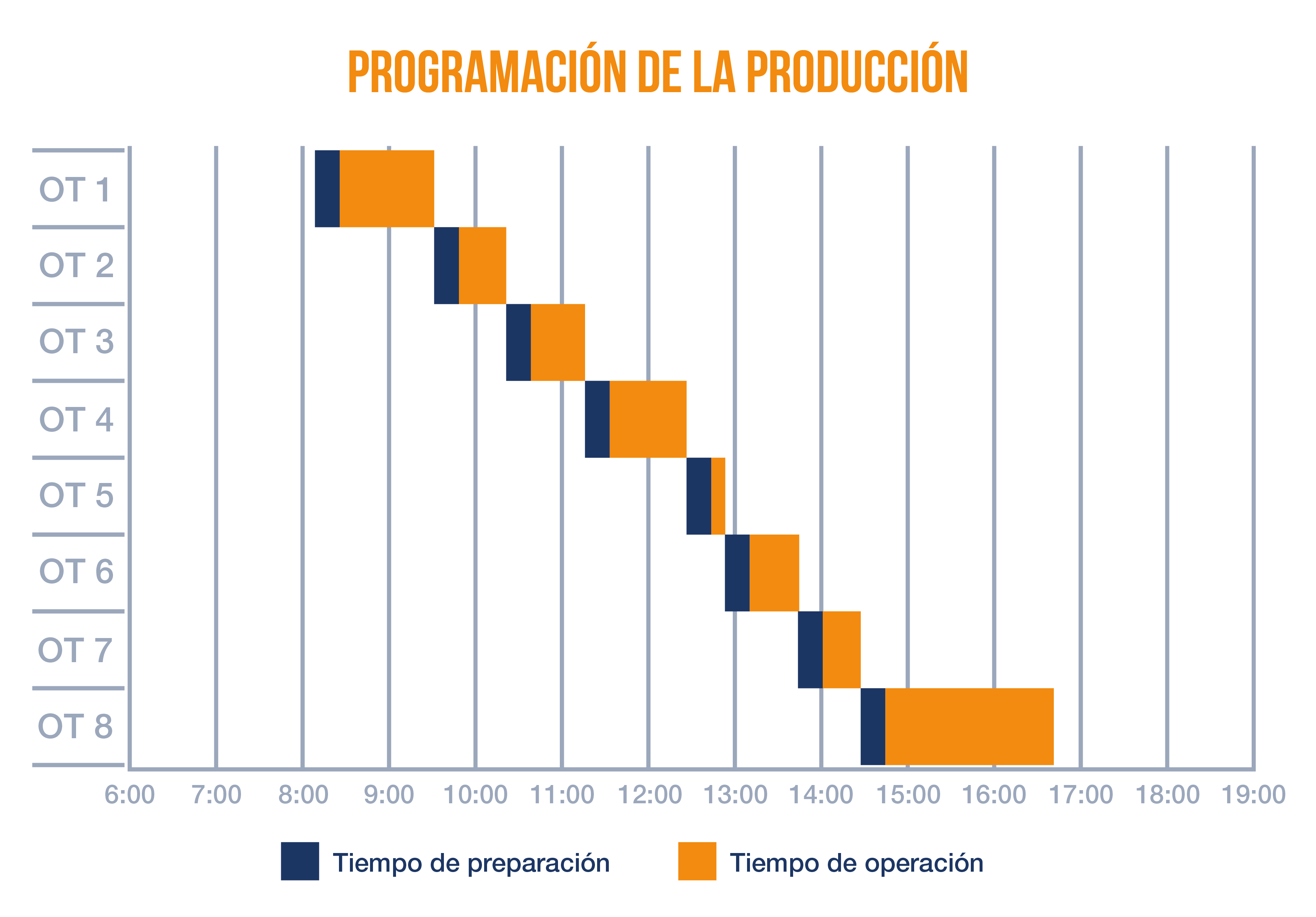
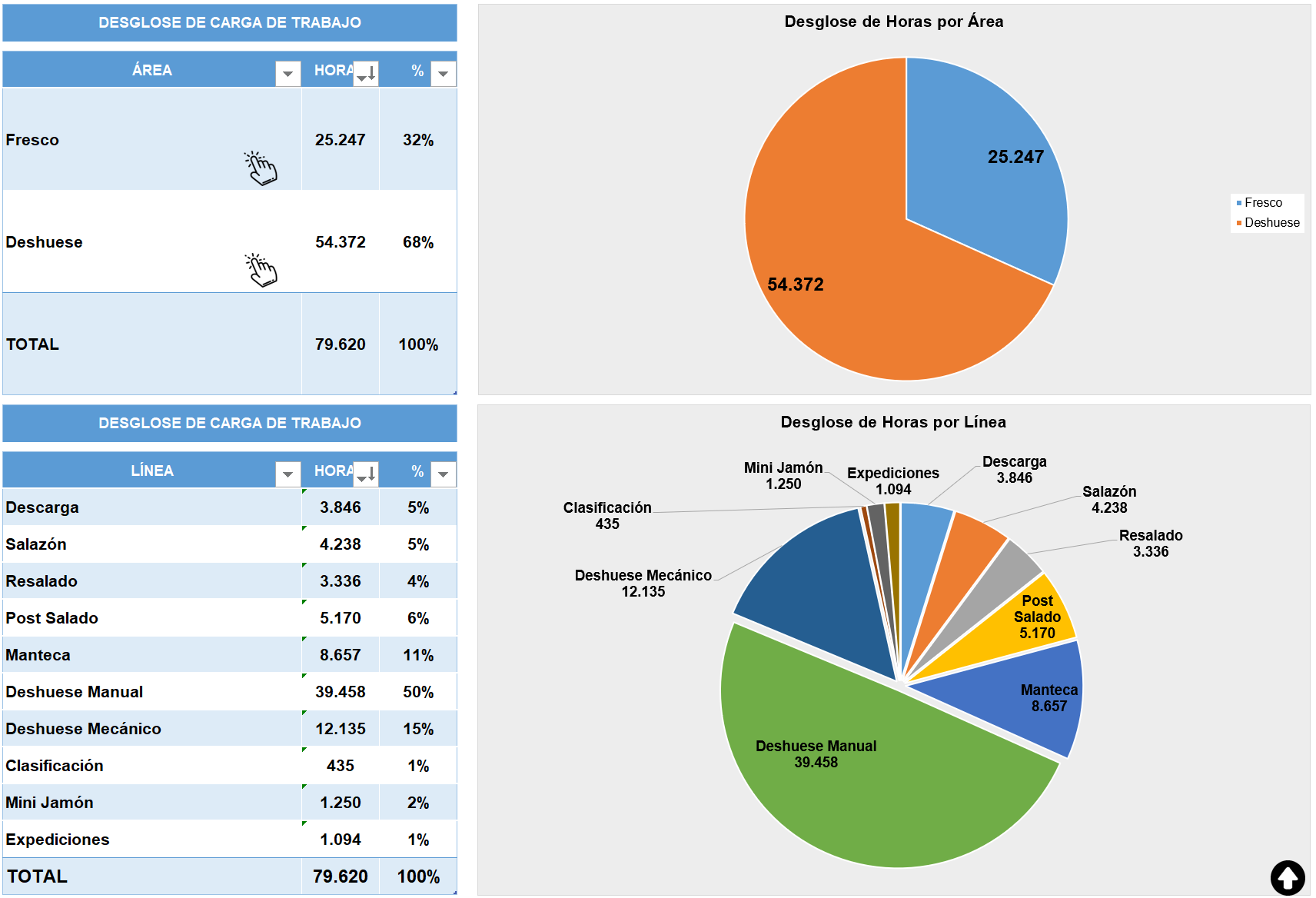
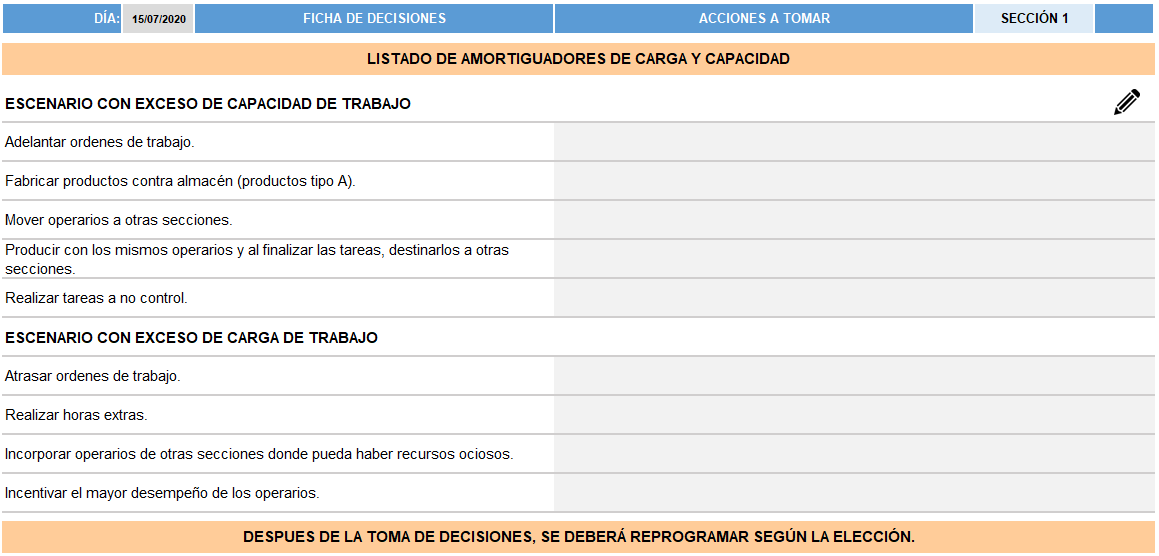
Objetivos
- Conocer de manera precisa la carga de trabajo y ajustar la capacidad a la misma con anticipación.
- Realizar los cálculos de manera ágil, con poca carga de datos y un sencillo análisis de la información. Para:
- Aumentar la capacidad de producción.
- Reducir los costes.
- Cumplir con los plazos acordados.
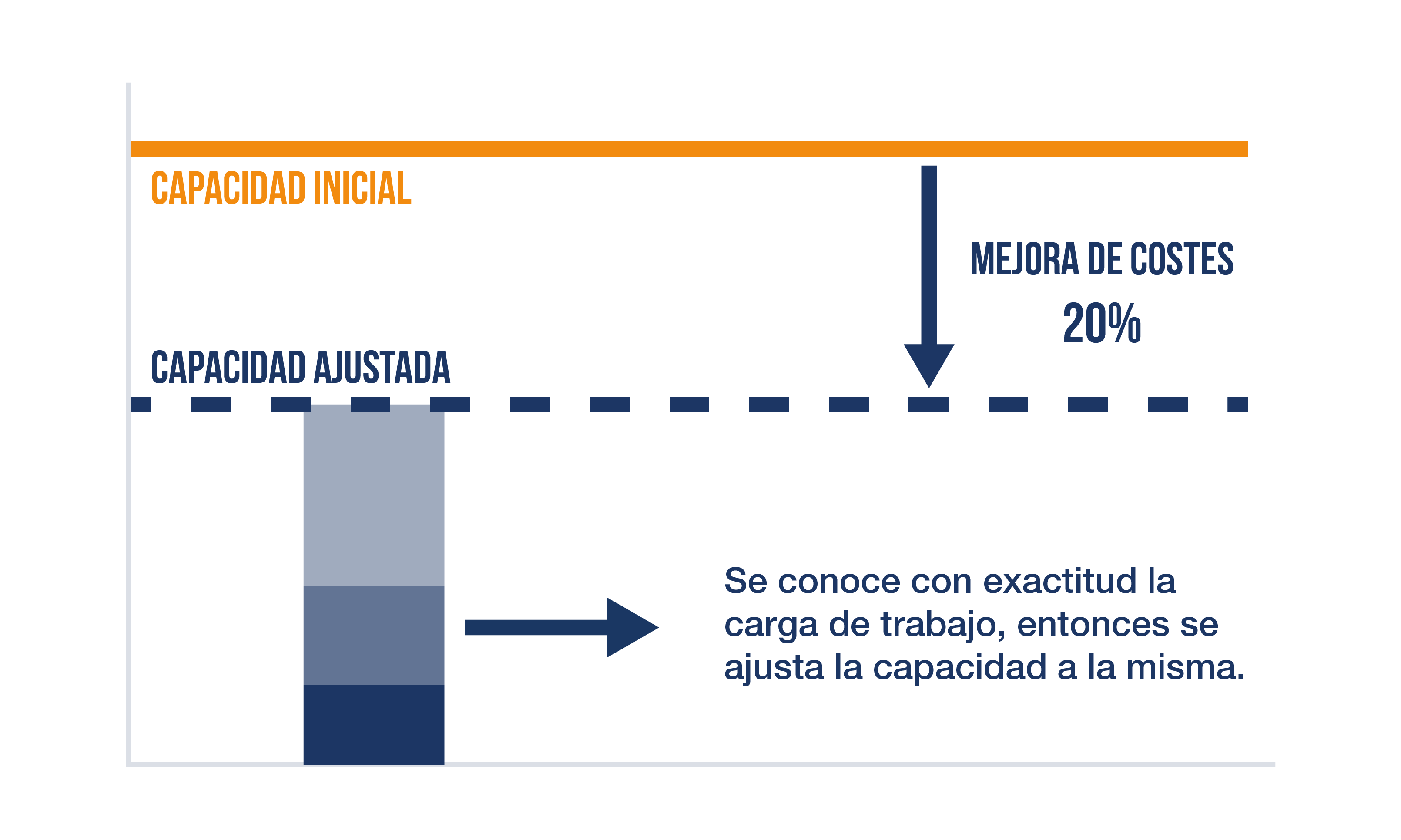
Indicadores de eficacia del proyecto
- Nivel de productividad.
- Cumplimiento de las entregas.
- Capacidad de producción.