PLANIFICACIÓN DE LA PRODUCCIÓN
CUMPLIMIENTO DE ENTREGAS Y COSTES
- Desarrollar un modelo de planificación y políticas comunes a todos los departamentos.
- Cumplimiento de la planificación: costes y plazos.
- Incremento de la capacidad de producción y mejora del nivel de servicio.
- Planificación ágil en función del mix de producción.
- PLANIFICAR ES GOBERNAR
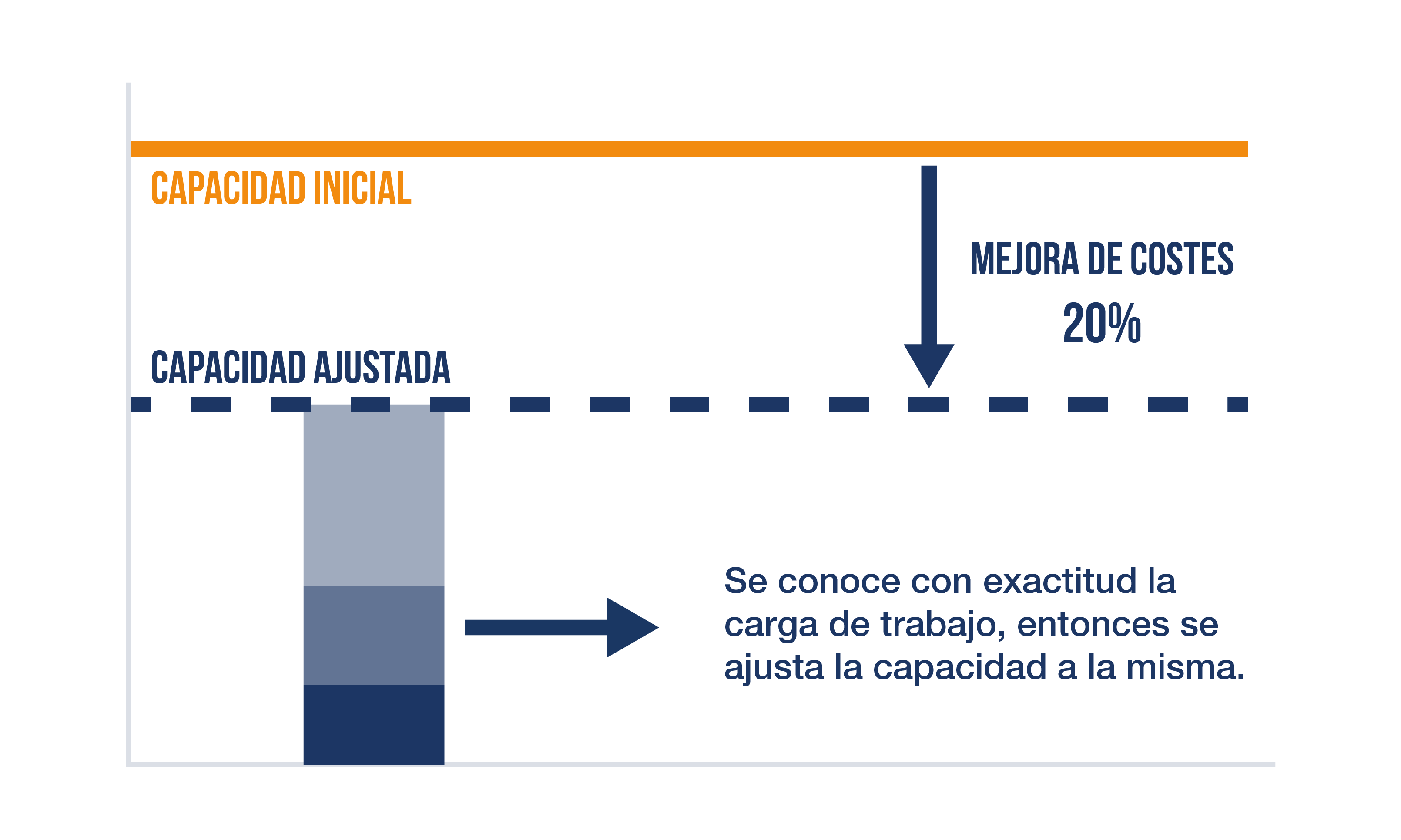
Conceptos previos
- Cuando se planifica la producción lo que determina es:
- Las entregas a los clientes (internos o externos).
- Y el coste al cual se harán estas entregas.
- De tal manera que es un factor determinante en la competitividad.
- ¿Qué debe tener en cuenta la planificación?
- Nivel 1 - Lo que sabes que sabes:
- Mix de producción a realizar, pedidos, etc.
- Capacidad disponible.
- Si te quedas en el Nivel 1, la planificación no sobrevivirá al primer encuentro con la realidad.
- Nivel 2 - Lo que sabes que no sabes:
- Todo aquello que no está en los planes que sabes que puede pasar pero que no sabes si va a pasar.
- Averías de máquina.
- Un repunte del absentismo.
- Urgencias de clientes y reprocesos.
- Un fallo de suministro crítico.
- Un periodo de baja demanda.
- Un pico de demanda fuera de la norma.
- ¿Qué hace la función planificación?
- En el ámbito de lo conocido – Nivel 1:
- Proponer la dotación de recursos necesarios.
- El orden o secuencia de producción.
- En el ámbito de lo aleatorio (imprevistos) – Nivel 2:
- Desarrolla los protocolos de reacción ante las perturbaciones de carga y de capacidad.
- Y se dota de los recursos para poder responder a dicha aleatoriedad.
- LAS PLANIFICACIONES NO SUELEN FUNCIONAR PORQUE NO SE SUELE PASAR DEL NIVEL 1.
Diagnóstico
- No se tienen tiempos estándar, se desconoce cuánto tiempo se tarda en hacer las tareas.
- No se dispone de una herramienta que permita planificar de manera ágil los trabajos entonces puede pasar lo siguiente:
- Se hace de manera manual o por intuiciones.
- Los comerciales se acaban haciendo con el poder y las decisiones de planificación y, entonces, lo que manda es la presión de los clientes.
- Los encargados demandan más recursos.
- Falta de formación:
- No se planifica teniendo en cuenta la saturación.
- No se planifican al detalle los cuellos de botella.
- Los mandos no saben cómo asignar los recursos.
- No se tienen en cuenta la multitud de imprevistos que pueden impactar en nuestra planificación, pero es inevitable que sucedan.
Efectos
- El desequilibrio entre carga y capacidad de trabajo es el mayor causante del despilfarro en fabricación. Lo cual tiene numerosas implicaciones y de alto impacto.
- Se aumenta la capacidad más de lo necesario debido al desconocimiento de la carga real de trabajo y a la incertidumbre.
- Aun así, faltan recursos para cumplir el plan y los compromisos acordados con los clientes.
- Por lo que los encargados solicitan más personal.
- Personal que tras esa “sobrecarga” de trabajo, se vuelve “totalmente necesario” para la normalidad.
- O se resuelve mediante sobrecostes por horas extra.
- Los puestos o máquinas cuellos de botella provocan esperas en los puestos anteriores o posteriores.
- Incluso, a veces, se quedan parados sin trabajo… siendo cuellos de botella.
- Y la producción que no hace el cuello de botella no se puede recuperar.
- Urgencias y continuas replanificaciones.
- Lo que provoca un movimiento continuo de operarios entre puestos sin posibilidad de anticipación.
- Y un exceso de cambios de máquina, formato y de trabajo.
- Lo que a su vez provoca iniciar trabajos sin asegurar las condiciones estándar.
- Generando interrupciones continuas.
- Traduciéndose en sobrecostes por ineficiencias por incidencias.
- Trabajos que se preparan y se comienzan, se pausan, y vuelven a prepararse y a continuarse posteriormente por falta de materiales y/o información.
- Operarios que, conociendo que la carga de trabajo asignada es baja, “estiran” el trabajo mediante ajustes y revisiones innecesarias, paradas, ausencias y baja actividad para que sea suficiente para acabar la jornada y no se le asignen más tareas.
- Los cambios de referencia no se planifican, por lo que siempre requieren un tiempo superior al estándar.
- Los pedidos no se agrupan generando lotes grandes de una misma referencia, por lo que se tienen más preparaciones de las que se debería.
- La fabricación no se ordena según criterios de eficiencia, por lo que no se optimizan los cambios ni la producción en función de la combinación óptima y la minimización de los tiempos de cambio y preparación.
- Y, además de lo anterior, del sobredimensionamiento de recursos, se incumplen los plazos de entrega.
- La fluctuación de la demanda que no se gestiona de manera ajustada provoca que los beneficios que se obtuvieron en periodos de saturación normal, queden mermados a causa de los periodos de baja carga de trabajo.
- El menor imprevisto hace que todo el trabajo de planificar sea inservible.
- AUSENCIA DE PLANIFICACIÓN ES AUSENCIA DE GOBIERNO
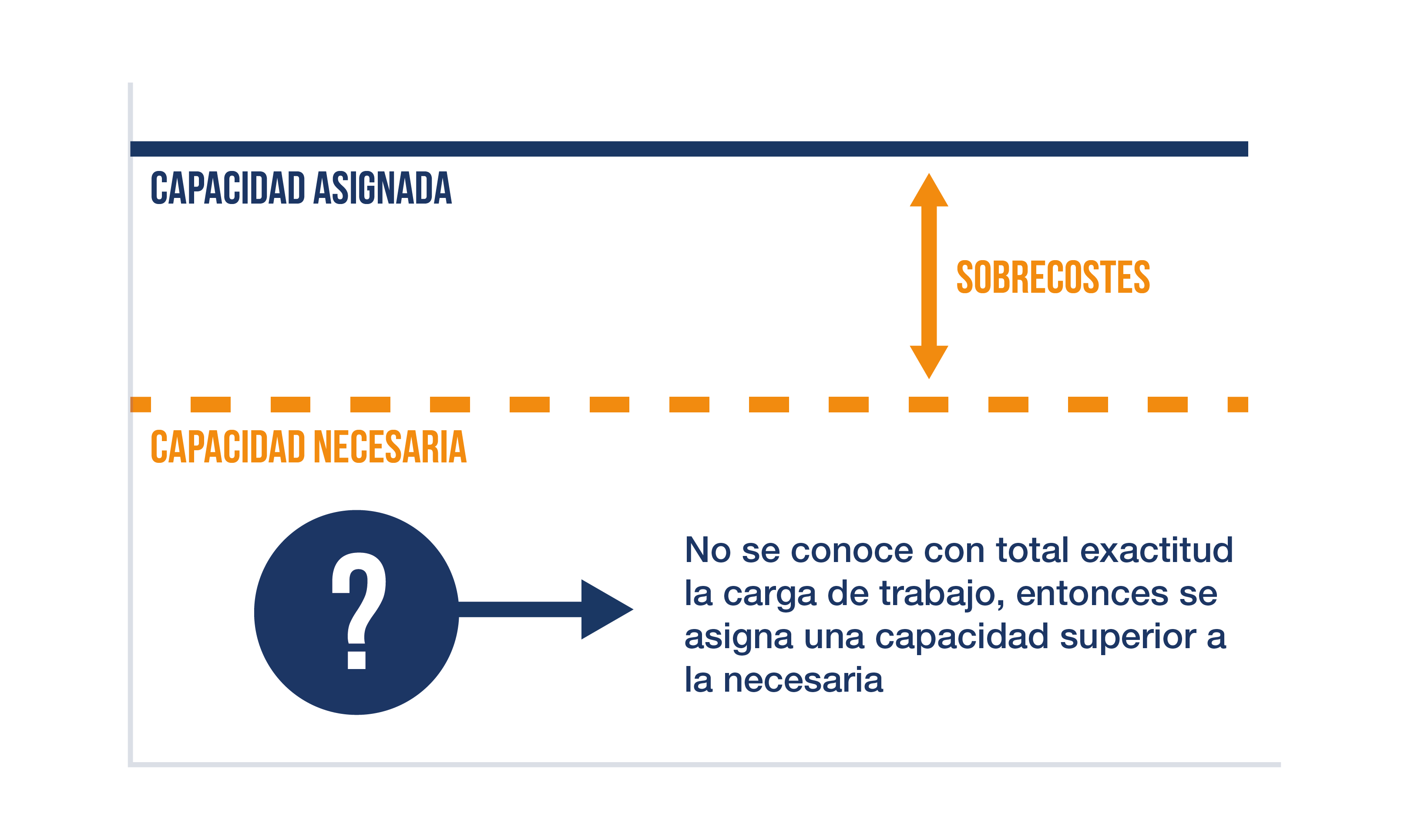
NECESIDAD Y PROPUESTA DE SOLUCIÓN
- Desarrollar un modelo de planificación y políticas comunes a todos los departamentos.
- Conocer de manera precisa la carga de trabajo y ajustar la capacidad a la misma con anticipación.
- Realizar los cálculos de manera ágil, con poca carga de datos y un sencillo análisis de la información. Para:
- Aumentar la capacidad de producción.
- Reducir los costes.
- Cumplir con los plazos acordados.
- Dotar a la fábrica de protocolos y recursos para no interrumpir el proceso ante imprevistos.
- Formación a los implicados.
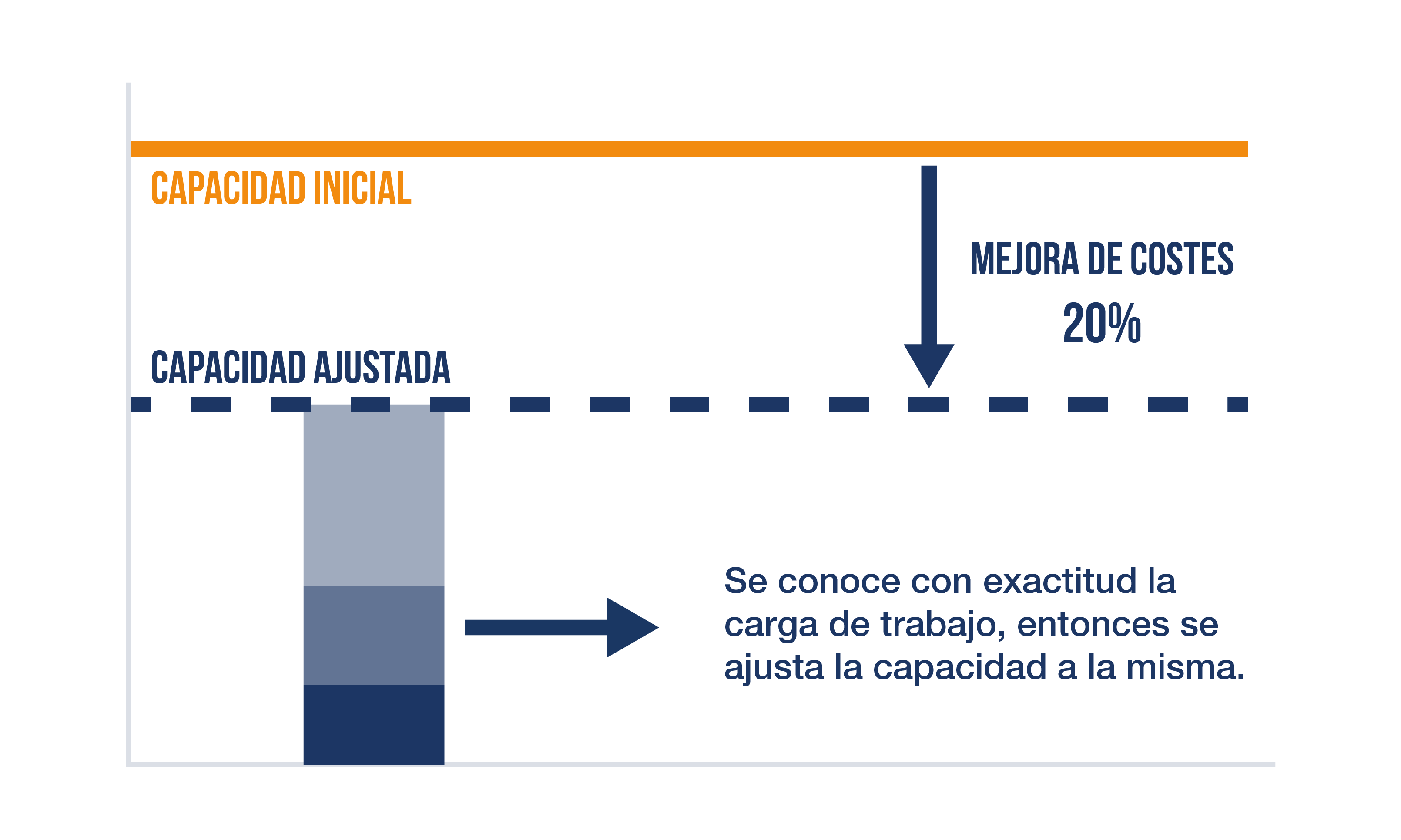
Indicadores de eficacia del proyecto
- Nivel de productividad.
- Cumplimiento de las entregas.
- Capacidad de producción.
Contacta con nosotros y mejora la productividad de tu industria a partir de una solución de alto impacto y bajo coste.
Compartir